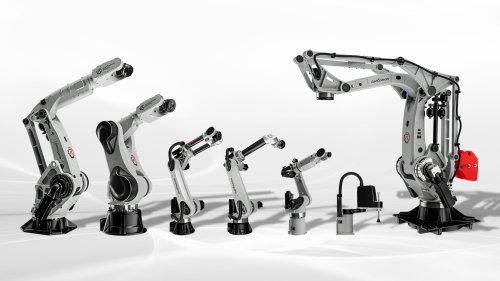
Articulated Robots
Articulated Robots
Articulated robots are characterized by their multi-axis joint structure, allowing for highly flexible movement in three-dimensional space. The design of an articulated robot arm enables precise execution of complex motion sequences, making them ideal for a wide range of industrial applications.
Their serially connected joints provide extensive reach and flexibility, allowing them to work efficiently in complex industrial robot cells. This combination of versatility, precision, and reliability makes articulated robots an essential component in modern industrial production, supporting tasks across diverse sectors with high efficiency and consistency.
Articulated robots are a fundamental part of automated production systems, providing precise, multi-axis motion for a wide range of tasks. Their jointed structure, often featuring rotary connections, allows for complex movements in three-dimensional space, making them ideal for assembly, welding, packaging, and material handling. These robotic arms for manufacturing are designed to handle both high-speed operations and delicate, precise tasks, integrating seamlessly into automated production lines.
The design of an industrial articulated robot is characterized by a flange at its end, facilitating the attachment of various end effectors, such as grippers, suction cups, and welding torches. This adaptability allows for a wide range of tasks, from electronics assembly to automotive welding. Modern articulated robots, often equipped with 5 or 6-axis arms, provide versatile movement suitable for various applications. They integrate advanced safety mechanisms, including force-torque monitoring and emergency stops, to ensure safe and precise operations. Connectivity with broader automation systems is achieved through industrial communication protocols like PROFINET and EtherCAT, allowing real-time interaction with sensors, machine controllers, and HMIs. Articulated robot manufacturers emphasize the importance of precise mechanics, adaptive control, and robust safety features, making these robots indispensable in high-speed, automated production settings.
Articulated robots are characterized by their multi-axis design, typically featuring four to seven rotary joints, which provide a high degree of flexibility and precision. Key features of articulated robots include extensive range of motion, high payload capacity, and precise control systems.
Their multi-joint configuration provides multiple degrees of freedom, allowing for complex path movements, joint interpolation, and accurate positioning. Advanced motion control systems, including servo motors, precision encoders, and direct-drive motors, enable precise path planning, speed control, and repeatable positioning, even in high-speed operations. Some models also include torque sensors and force control systems, enhancing their ability to handle delicate tasks and maintain consistent force during assembly or welding.
Articulated robots also have high load-to-weight ratios, allowing them to handle a wide range of payloads, from small components to heavy parts, with consistent accuracy. This is supported by lightweight, high-strength materials like aluminum alloys and carbon fiber composites, which reduce inertia and improve acceleration.
Many models are equipped with integrated sensors and vision systems, providing real-time feedback for adaptive operations, collision detection, and precise part positioning. This allows them to adjust their movements based on the workpiece and environment, reducing errors and improving process reliability.
Additionally, articulated robots feature compact bases, making them suitable for crowded factory floors.
Their modular design allows for flexible integration into larger automation systems, supporting seamless communication with machine controllers, sensors, and human-machine interfaces through industrial communication protocols like PROFINET, EtherCAT, and Modbus.
Articulated arm robots, particularly articulated industrial robots, are pivotal in enhancing industrial automation. Their sophisticated multi-axis design endows them with exceptional flexibility and precision, allowing them to perform complex, three-dimensional tasks with ease. These robotic arms are indispensable in operations that demand intricate movements and accuracy. A robotic welding arm, for example, demonstrates the capability to execute precise welds in challenging positions, thereby improving efficiency and consistency in manufacturing processes. The versatility of articulated robots makes them invaluable assets across various industries, contributing significantly to optimized productivity and quality.
Articulated robots offer several advantages, notably their high precision and repeatability, which are crucial for industries such as electronics and automotive manufacturing. They are capable of managing a wide range of payloads, from small components to heavy parts, while maintaining precise control. Additionally, these robots enhance efficiency by reducing cycle times and increasing throughput in high-volume production environments. Despite their extended reach, articulated robots possess a compact footprint, making them ideal for crowded factory floors.
However, like any advanced technology, articulated robots come with certain challenges. Their sophisticated design can lead to higher initial investment costs and may require more frequent maintenance to ensure reliable performance. The complexity of their multi-axis movement also demands specialized programming and operator training, which can add to operational expenses. Nevertheless, these considerations are often outweighed by the long-term benefits of improved productivity, precision, and flexibility in automated manufacturing.
With advanced control systems, they can integrate with sensors and vision systems for adaptive tasks, enhancing automation flexibility. These robots also improve workplace safety by reducing human exposure to dangerous environments and repetitive tasks, providing long-term cost savings.
Choosing the right articulated robot for a specific application involves several important considerations.
One of the primary factors is the number of axes, which determines the robot's flexibility and range of motion. For complex tasks requiring full 3D movement, 6 axis robot arms are often preferred, while 5 axis articulated robots may be sufficient for simpler operations with lower motion complexity.
Payload capacity is another critical factor, as the robot must be capable of handling the weight of the workpiece and any attached end effectors, such as grippers or welding torches. This includes accounting for dynamic forces during rapid acceleration and deceleration.
Reach and workspace are also essential, as the robot must be able to access all necessary points within its operating area without excessive reconfiguration. The choice of reach is often influenced by the size of the parts being handled and the layout of the production cell.
Precision and repeatability are crucial for tasks requiring high accuracy, such as electronics assembly or precision welding. Articulated robots with high-resolution encoders and advanced motion control systems can achieve tight tolerances, ensuring consistent quality.
Speed and cycle time are also important for high-volume production, where reducing idle time can significantly improve overall throughput. This is often a trade-off with precision, as faster movements can increase positioning errors.
Finally, safety features such as force-torque sensing, safe motion limits, and emergency stop systems are critical for ensuring worker safety and reducing downtime in automated environments.
Articulated robots are essential in modern manufacturing, offering precise, multi-axis motion and flexibility for a wide range of applications.
6-axis robot arms are particularly common in the automotive industry, where they are used for spot welding, body panel assembly, painting, and complex material handling. These robots provide extensive reach, high torque, and precise path control, making them ideal for assembling complex structures and performing tasks that require continuous, multi-directional movements.
In electronics manufacturing, articulated robots are critical for high-speed assembly, micro-soldering, and component placement. Their six degrees of freedom allow for accurate positioning and repeatability, ensuring the precise handling of delicate components and circuit boards.
5-axis articulated robots are widely used in the food and beverage industry for high-speed picking, packaging, and palletizing. These robots are designed for rapid, repetitive tasks, where fewer degrees of freedom provide faster cycle times and simplified control, while maintaining the strength and precision needed for consistent product handling.
Articulated robots also play a role in the medical field, where precise, multi-jointed arms enable minimally invasive procedures with sub-millimeter accuracy, enhancing surgical outcomes and patient recovery times.
The evolution of articulated robot design is significantly influenced by advancements in technology and industrial requirements.
A pivotal development is the incorporation of artificial intelligence (AI) and machine learning (ML), facilitating robots in adjusting to dynamic production settings, optimizing their movements, and enhancing process efficiency. This allows programmable robotic arms to make instant decisions, reduce cycle times, and boost productivity.
Additionally, the rise of collaborative robots (cobots), featuring advanced safety systems such as force sensors and motion monitoring, is noteworthy. These systems ensure safe cooperation with human operators in shared spaces.
The implementation of lightweight materials and direct-drive motors enhances the speed, precision, and energy efficiency of industrial robot arms, minimizing weight and inertia.
Moreover, articulated robot manufacturers are focusing on equipping robots with sophisticated vision systems and adaptive grippers, allowing for versatile task execution in flexible manufacturing environments without the need for extensive reprogramming.
autonox Robotics offers a wide range of robotic mechanics, from compact SCARA systems to fully articulated 6-axis robots. These platforms are known for their high flexibility and integrated media supply, making them ideal for a wide variety of automation tasks. Whether you’re entering the world of robotics or looking to optimize your existing processes, we provide the perfect robotic solutions for your needs.
2 DoF (Degrees of Freedom): Integrated media supply available, suitable for wall mounting when vertically aligned).
4 DoF: Optional integrated tool changing system (ATS), fourfold media supply, flexible flange wiring, suitable for floor, wall, and ceiling mounting (vertical hub-rotation module).
3 DoF: Compact units for precise positioning, suitable for all mounting types (floor, wall, ceiling, angle).
3 DoF: Compact design with integrated media supply, flexible mounting options (floor, wall, ceiling, angle).
4 DoF: Optional with customized compensation dataset (in preparation), same flexible mounting options.
5 DoF: Also available with a planned compensation dataset; suitable for floor, wall, ceiling, and angle mounting.
6 DoF: The most versatile solution, featuring advanced media integration and optional add-on modules for seamless compatibility with various control systems.
Our articulated robotic mechanics provide maximum flexibility and adaptability, ensuring efficient integration into diverse automation environments. These robots are ideal for companies looking to enhance productivity, precision, and quality in their manufacturing processes. With a wide range of mounting options and advanced features, autonox articulated robot mechanics are the smart choice for scalable, future-proof automation.